When it comes to optimizing the energy efficiency of our compressed air system, we at HUESKER rely on highly efficient screw compressors and energy-saving nozzles – so we benefit from high energy efficiency with savings of up to 70%. This reduces costs and, at the same time, protects the environment.
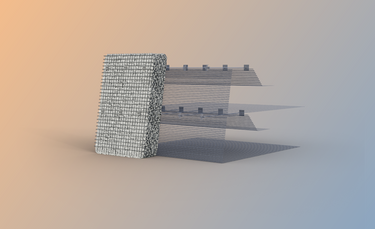