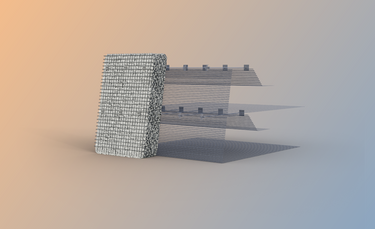
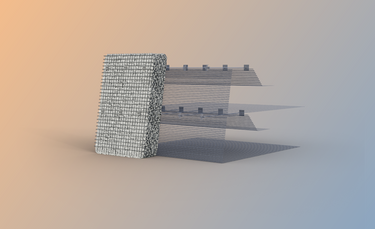
Yarn and fabric waste cycle
Unfortunately, a certain amount of unavoidable waste in the form of yarn and fabric remnants is always generated during the production of textiles on our weaving machines. Although efficient planning and the appropriate machine settings reduce waste, we cannot avoid it completely. To ensure that the waste does not simply end up in a landfill, we have taken on the task and responsibility of utilizing these remnants or waste in a sensible way. The residues that we cannot utilize are valuable raw materials and can be fed into the circular economy and the reprocessing cycle to save resources.
Rubbish to us - useful and valuable to others
Edge trimmings from produced goods, yarn remnants after bobbin or warp changes, fabric remnants after article changes, or during sample production in the laboratory - all this waste is unfortunately unavoidable. However, behind these yarn, fabric, and waste cuttings or empty yarn tubes are valuable raw materials such as PET, PVA, PP, and aramid. With these high-quality raw materials and high-quality fibers, new products can see the light of day after recycling and reprocessing. We work together with our partners Altex, Barnet Davy, and the Haus Hall sheltered workshop.
Collecting, separating, sorting, reusing
During ongoing production, the fabric edges are cut off at the Raschelei extraction system, extracted, and collected in a reusable container (previously a cardboard box).
We pass on our yarn remnants on tubes to the Haus Hall workshop for recycling and separation. The employees removed the yarn remnants from the tubes for us and filled the separated yarn into the mesh boxes. We are able to recycle some of the empty tubes. The yarn remnants are sorted and sent to Altex or Barnet Davy.
A win-win situation
As soon as 44 full pallet cages have been reached, we will organize free collection directly from us or Haus Hall on an alternating basis. For this purpose, we will prepare the delivery note, including the calculated net weight. As part of the collection of the full goods, 44 empty pallet cages are unloaded by Altex - an efficient deposit system. The textile recycling companies Altex and Barnet Davy process the materials for targeted reintroduction into the market, such as fleece, which can be recycled as insulation material, for example.
Continuous improvement - ongoing optimization for greater sustainability
Until a few years ago, the yarn and fabric remnants were still collected in cardboard boxes. These were stored on shelves. As soon as the shelves were full, the boxes were transported by a haulage company to the recycling company, where they were disposed of. It was not only the waste that was problematic but also the fact that the boxes could not be stacked. There were space problems in the warehouse, and the lead times for collections were difficult to plan. Plus, HUESKER bore the transport costs. We soon realized that we could do better!
The only advantages for everyone
What initially seemed like a small change turned out to be a big improvement in terms of volume! We save over €15,000 per year in packaging and transport costs.
A further advantage is higher efficiency in the rinsing process thanks to the reusable boxes in the extraction systems! A third more filling quantity in the boxes - thus longer running times for the machines and less effort for the machine operators.
I am very happy about this successfully functioning closed-loop system, as everyone involved benefits from it. It has shown that opportunities for improvement need to be seen, addressed, and then simply tackled! It was also great to see how the discussions and coordination led to a lot of support and positive feedback!
Reaching the top of the mountain alone is doable, but together as a team it's easier. Many hands, make light work!
Yours, Martin